Materials & Fracture
The selection of materials is a critical step in the design process, and it directly affects the performance, cost, and reliability of the final product. The choice of material should be based on several factors, including the functional requirements, operating conditions, manufacturing process, and environmental impact. The mechanical, thermal, electrical, and chemical properties of materials, as well as their availability, cost, and sustainability, should be carefully evaluated to ensure the right material is chosen for the application.
For example, consider the chassis of a car. It is designed to support the engine, passengers and other components. It is also designed to absorb impact in the event of an accident to protect the passengers inside. Given these requirements, metal is a good candidate as the manufacturing material - it has a higher ultimate strength and can stretch to carry more load. For this particular application, ceramics would not work well due to their brittlness, higher density and lower ultimate strength. The figure below shows how the chassis absorbs the shock and load during an accident. Old and new versions of the car are compared to better understand how much the development has improved.
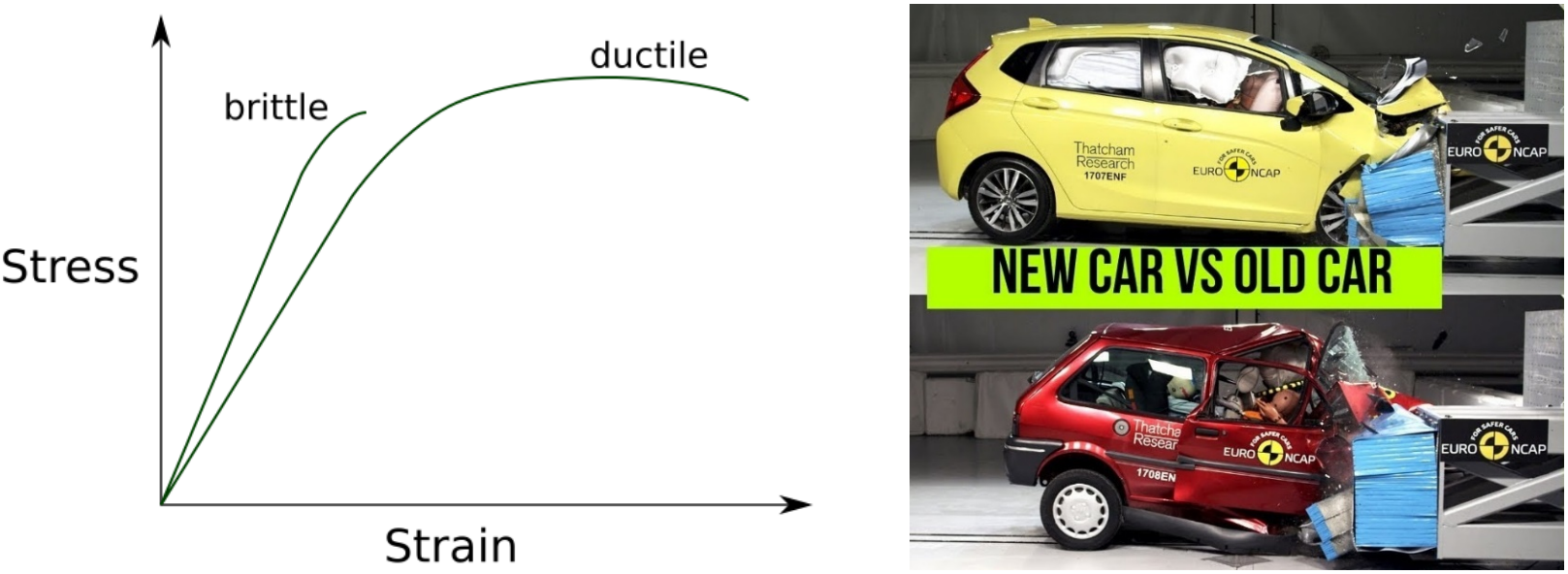
The ability of ductile materials to elongate is compared with that of brittle materials. This ability to stretch and absorb impact is used in cars. The cabin in the old car is heavily deformed compared to the new version - keeping the passengers safe (from www.motor1.com).
Some of the key requirements for material selection in design are listed below.
- Material properties: The material should be able to meet the functional requirements of the product, such as mechanical strength, stiffness, toughness, and wear resistance, as well as thermal, electrical, and chemical properties.
- Availability and cost: The material should be readily available and cost-effective for the application, and should not be subject to supply chain disruptions or price fluctuations.
- Operating conditions: The material should be able to withstand the operating conditions, such as temperature, pressure, humidity, and exposure to chemicals or radiation.
- Regulatory compliance: The material should meet regulatory requirements, such as safety, health, and environmental standards, and should not pose any risks to human health or the environment.
- Sustainability & Environmental impact: The material should be sustainable, such as using recycled materials or renewable resources, to reduce waste and conserve natural resources. It should also have minimal environmental impact, such as low carbon footprint, low toxicity, and high recyclability.
Key properties
Material selection is based on the design requirements and the mechanical properties of the material. Some of the most relevant properties of a material are listed below.
- Strength: The material should be strong enough to withstand the loads and stresses that it will be subjected to during use.
- Stiffness: The material should have sufficient stiffness to maintain its shape and resist deformation under load.
- Toughness: The material should be able to absorb energy without fracturing or breaking under impact.
- Hardness: The material should be resistant to scratching, abrasion, and wear.
- Ductility: The material should be able to deform under stress without fracturing.
- Thermal properties: The material should have appropriate thermal conductivity, expansion coefficient, and melting point for the intended application.
- Electro-mechanical properties: The material should have appropriate electrical conductivity, insulation and magnetic permeability and so on, for the intended application.
- Corossive resistance: The material should be able to resist the effects of chemical reactions and environmental exposure.